Blog
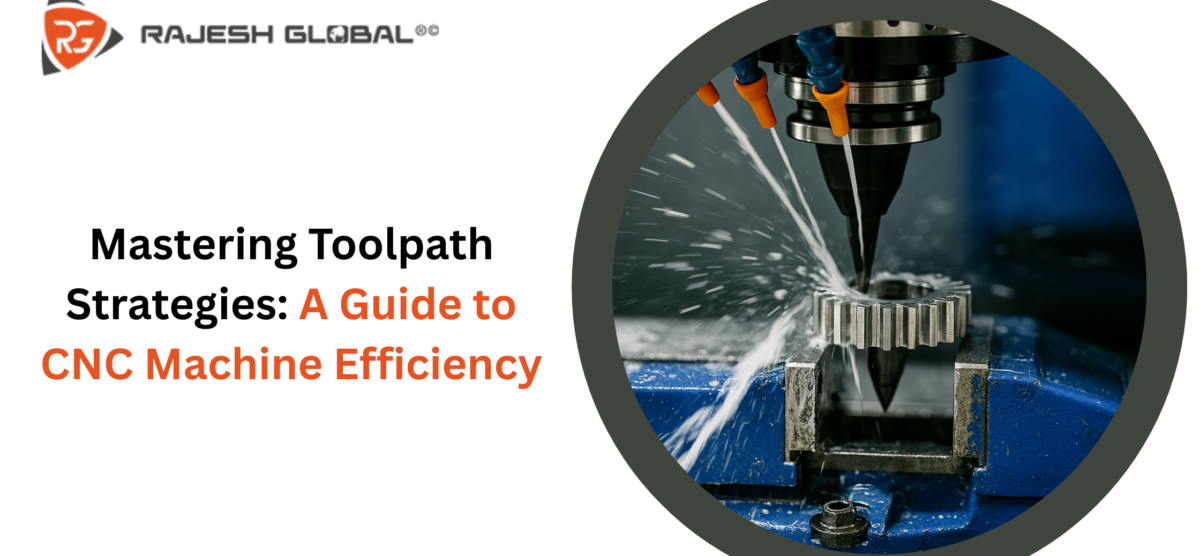
Mastering Toolpath Strategies: A Guide to CNC Machine Efficiency
What if you could increase your CNC machine productivity by up to 50% with just a few tweaks to your workflow? Understanding toolpath strategies is the key to unlocking that potential. CNC machining has revolutionized the manufacturing landscape, allowing for precision and efficiency that were previously unimaginable. And toolpath strategies are one of the best ways to maximize your CNC machine’s potential.
This guide will delve into the intricacies of toolpaths, exploring various strategies, optimization techniques, and practical applications to help you elevate your machining game.
What is a Toolpath?
Contents
A toolpath in CNC machining is the exact route a cutting tool takes while working through a piece of material. Think of it as a carefully plotted journey that dictates every twist, turn, and depth level the tool will navigate. The design and execution of a toolpath significantly influence the efficiency of the machining process and the accuracy of the final product. A well-planned toolpath can enhance surface finish, extend tool life, and optimize material removal rates.
Types of Toolpath Strategies
Diving into the world of CNC machining, you’ll encounter various toolpath strategies tailored to different applications. Each strategy has unique benefits that can enhance efficiency:
- Zig-Zag Toolpath: This strategy is ideal for pocketing and profiling operations. By minimizing tool retractions, zig-zag toolpaths optimize cutting efficiency and reduce cycle times.
- Radial Toolpath: Best suited for machining cylindrical or contoured surfaces, radial toolpaths ensure consistent tool engagement and smooth material removal, which is essential for achieving high-quality finishes.
- Contour Toolpath: Known for its versatility, the contour toolpath follows the outline of a part with precise control over tool engagement. This method excels in machining complex geometries while maintaining tight tolerances.
- Spiral Toolpath: Effective for high-speed machining of deep cavities, spiral toolpaths maintain a consistent cutting load, reducing tool wear and machining time significantly.
- Parallel Toolpath: Employed primarily for flat surfaces, parallel toolpaths optimize spacing to minimize overlap and maximize machining efficiency. This method is particularly useful when working with large areas that require uniform treatment.
Optimization Techniques
To truly master CNC machining, one must delve into optimization techniques that enhance toolpath strategies. Here are some key methods that can significantly improve efficiency:
- Adaptive Clearing: Utilizing dynamic algorithms, adaptive clearing optimizes tool engagement and chip load to maintain constant cutting forces throughout the operation. This technique minimizes tool wear and reduces the risk of breakage.
- Trochoidal Milling: By employing circular toolpaths with small radial stepovers, trochoidal milling reduces cutting forces and vibrations. This results in improved surface finishes and extends tool life.
- Rest Machining: This technique targets areas that were not machined in previous operations, allowing for efficient material removal without unnecessary passes over already processed sections.
- Toolpath Smoothing: Implementing smoothing algorithms reduces abrupt changes in direction during cutting. This not only improves surface finish but also enhances dimensional accuracy by minimizing deviations.
Advanced Toolpath Strategies
As technology advances, so do our capabilities in CNC machining. Incorporating sophisticated strategies can lead to remarkable improvements in performance:
- High-Speed Machining (HSM): This technique focuses on achieving higher feed rates while maintaining precision. HSM is particularly beneficial when working with hard materials where traditional methods may falter.
- Artificial Intelligence (AI) and Machine Learning (ML): These technologies are at the forefront of revolutionizing CNC operations. By analyzing vast datasets from previous machining processes, AI can predict optimal paths for new projects based on historical performance metrics. This data-driven approach not only enhances efficiency but also allows for continuous improvement as more data is gathered.
- Deep Learning Algorithms: These algorithms excel at handling complex problems by learning from historical data to refine predictions about optimal toolpaths over time. They adapt dynamically to changing conditions during machining processes, ensuring that operators can achieve their desired outcomes efficiently.
Practical Applications and Case Studies
To bring these concepts to life, let’s explore some real-world applications where effective toolpath strategies have made a significant impact:
- Aerospace Component Manufacturing: In aerospace applications where precision is paramount, manufacturers have adopted contour and spiral toolpaths to produce intricate parts with minimal waste. The use of adaptive clearing has further enhanced their ability to maintain consistent quality while reducing cycle times.
- Automotive Industry Innovations: Automotive manufacturers have leveraged trochoidal milling techniques to improve efficiency when machining complex engine components. By reducing cutting forces through optimized paths, they have seen substantial gains in both productivity and part quality.
- Medical Device Production: In the medical field, where tolerances are critical, companies utilize advanced CAM software to simulate various toolpaths before actual machining begins. This preemptive approach allows them to identify potential issues early on, saving time and resources while ensuring compliance with stringent quality standards.
Conclusion
Mastering toolpath strategies is essential for anyone looking to enhance their CNC machining capabilities. By understanding different types of toolpaths and implementing optimization techniques, you can significantly improve your machine’s efficiency and output quality. The integration of advanced technologies such as AI and machine learning further empowers machinists to stay ahead in an ever-evolving industry landscape.